Showing 12 results for Mechanism
Mehryab A., Arabi H., Tamizifar M., Seyedein S.h., Razazi M.a.,
Volume 2, Issue 1 (3-2005)
Abstract
In this research, the mechanism of joining three sheets of metals, i.e. brass-steel-brass, by cold roll welding process has been studied. For this purpose, the two surfaces of steel sheets were roughened with stainless steel wire brush by different amounts, then the brass sheets were put on both sides of the steel sheets, before they were subjected to cold roll process. During rolling, peaks of the asperities on the surfaces of the steel sheet were pressurized, i.e. deformed, much more than that of trough. Hence, more hardening due to formation of higher dislocation density in the peaks regions were detected in comparison to the trough regions. Therefore, due to the differences in the amounts of work hardening occurred during cold rolling in the peaks & trough of the scratches and also due to the nature of the rough surfaces of the steel sheets, which causes the smooth surface of soft brass sheets laied over the rough surface of the steel sheet to be shappend according to the profile of the steel sheet scratches during cold rolling, mechanical locking occurred at the interface of brass & steel sheets. In addition, while the extrusion of brass took place through cracks within the surface of hardend peaks and metal bonding occurred on the contact points of the brass sheet & the vergin steel. Therefore, it seems two mechanisms were in operation is making a suitable joining between the sheets. One was a locking mechanism due to the roughness of the steel sheets & the other was bonding mechanism due to the bonding between the peak points of the scratches &soft brass surface. The strength of the bonded points in the interface were later increased by annealing the composite, so that by annealing the samples within the 500-900°C range for aperiod of 1 1/2 hr the interface strength increase substantially. The results of peeling test indicated that the interface strength of the samples annealed at 700°C or more increased so much that the brass sheet toms during peeling & the fracture did not pass through the interface.
Zhang S.,
Volume 2, Issue 3 (9-2005)
Abstract
Hydration behavior and antioxidising effect of aluminium (AI) powder has been investigated. Bayerite Al (OH) 3 product layers formed on Al in pure water at 25-45°C were porous, so the hydration rate, although very slow at 25°C, increased rapidly with increasing temperature from 25 to 45°C. On further increasing temperature from 45 to 95°C, initial hydration rate increased, but changed little over long hydration periods due to formation of denser and more continuous product layers. At 100?C, due to rapid water-evaporation, hydration product layers (composed of Al (OH)3 and a small amount of boehmite AlO (OH) became detached from the Al surfaces, so offering less protection, so that the hydration rate of Al increased markedly. The presence of MgO or calcium aluminate cement (CAC) in water did not change the hydration product, but greatly accelerate the hydration rate of AI. Addition of even a small amount (e.g. 0.25 wt% of Al amount) of MgO or CAC to water accelerated significantly the hydration of Al, and with increasing level of MgO or CAC, the hydration extent increased markedly. Sol-gel Si02 coatings on Al were useful in improving the hydration resistance of Al, and did not have a negative effect on the behavior of Al as an antioxidant.
S.h.r. Fatemi Nayeri, J. Vahdati Khaki, M. R. Aboutalebi,
Volume 6, Issue 1 (3-2009)
Abstract
Abstract:A combination of mechanical activation and Differential Thermal Analysis (DTA) together with X-Ray
Diffraction (XRD), and various microstractural characterization techniques were used to evaluate the starting reaction
in the combustion synthesis of TiC-Al2O3 composite in TiO2-Al-C system. The mechanical activation was performed
on the mixtures of two components of TiO2/Al, Al/C and TiO2/C and then the third component was added according
to the stoichiometric reaction for 3TiC+2Al2O3 composite formation. The powder mixtures were heated up to 1450 °C
under Argon atmosphere at a heating rate of 10 °C/min. The combustion synthesis temperature was observed to
decrease from 962 °C to 649 °C after milling of TiO2/Al mixture for 16 hr. On the contrary, the mechanical activation
of Al/C and TiO2/C mixtures for 16 hr made the reaction temperature increase to 995 °C and 1024 °C, respectively.
The decrease in reaction temperature as a result of milling the TiO2/Al mixture could be due to an increase of TiO2
and Al interface area as confirmed by TEM micrographs and XRD patterns of milled powder mixture. In addition, DTA
experiments showed that for the sample in which TiO2 and Al were mechanically activated the reaction occurred at
the temperature even lower than that of Al melting point.
M. Nusheh*, H. Yoozbashizadeh,
Volume 7, Issue 2 (6-2010)
Abstract
Abstract:
the competition between the precipitation of cobalt ions and evolution of hydrogen gas on the cathode surface during
the reduction process in a sulfate bath, investigation on the mechanism of metal precipitation is of great importance.
In the present work, study on the kinetics of cobalt electrowinning and the mechanism of the involved reactions have
been carried out. The obtained results, confirm the mechanism of cobalt precipitation by depletion of hydroxides. The
effects of temperature and scan rate parameters were studied on electrowinning of cobalt by cyclic voltammetry
technique. The diffusion coefficient and rate constant of the reactions were measured and calculated by performed
experiments.
Nowadays cobalt is mostly produced through the electrowinning process of sulfate solutions. Regarding to
H. Rafiee*,, S. Rastegari, H. Arabi, M. Mojaddami,
Volume 7, Issue 4 (10-2010)
Abstract
Abstract:
activity gas diffusion process has been investigated in this research. Effects of coating temperature and aluminum
concentration in powder mixture on formation mechanism were studied using optical and scanning electron
microscopes, EDS and X-ray diffraction (XRD) techniques. For this purpose two different packs containing 1 and 2
wt% aluminum powder, were used for coating the samples at two temperatures, 850ºC and 1050ºC. The ratio of Al to
activator was kept constant in both packs. By increasing the Al content in high activity powder mixture, the
concentration of diffused Al increased in the coating layers, and the thickness of coating increased. At 1050ºC as the
rate of diffused Al to the interdiffusion zone increased, this zone gradually transformed to outer coating phases. At
850ºC coating formed by inward diffusion of Al, but at 1050ºC it was initially formed by inward diffusion of Al followed
by outward diffusion of Ni.
Formation mechanism of an aluminide coating on a nickel base superalloy IN738LC via a single step high
M. Rezvani,
Volume 8, Issue 4 (12-2011)
Abstract
The effect of Y2O3, CeO2, P2O5, ZrO2 and TiO2 in single, double and triple form on crystallization mechanism of Li2OAl2O3- SiO2(LAS) glass-ceramic system was investigated .The nucleation and crystallization peak temperatures of optimized samples in each group were determined by Ray & Day method .The crystalline phase was determined by the X-ray diffractometery .The micro-structure of the samples was studied by SEM techniqe .Crystallization activation energy ,E, and kinetic constants(n ,m) were determined by differential thermal analysis (DTA) through Marotta and Augis-Bennet methods .According to the results ,the Avrami constants(m ,n) derived from the Marotta and Augis- Bennett, glasses containing both ZrO2 and TiO2 nuclei were showed bulk crystallization .The crystallization mechanism of specimens containing ZrO2, TiO2 and CeO2 in the triple nuclei series represent two-dimensional bulk crystallization .By comparison of Avrami constants and activation energy of crystallization of optimized samples with other results they gave much lower value of E(255.5 kJ/mol) and higher value of n in 4.38.The lattice constants of the main phase( -eucryptite solid solution)in samples were determined according to the XRD results
M. Sheikhshab Bafghi, M. Karimi, M. Adeli,
Volume 10, Issue 4 (12-2013)
Abstract
In the present study, reduction of zinc oxide from the pellets made of steelmaking electric arc furnace dust has been investigated. Effects of such parameters as the type of carbon material (graphite, coke and charcoal) as well as time and temperature on the reduction reaction have been examined. The reduced (dimensionless) time method was applied to perform a kinetic analysis of the system. Experimental results showed that increasing the temperature in the range of 925-1150°C results in a remarkable increase in the reduction rate. It was also shown that the reduction process is controlled by chemical reaction. Meaningful difference in the activation energy values calculated for reduction with graphite (24.75 kcal/mol), coke (18.13 kcal/mol) and charcoal (11.52 kcal/mol) indicate the predominant role of chemical reaction (carbon gasification) in the overall reaction rate and its rate-controlling mechanism. Carbothermal reduction of pelletized EAF dust proved to be an efficient reduction method, so that above 90% reduction was achieved in about one hour at temperatures around 1100°C.
H. Shalchian, A. Farbod, H. Beygi, S. A. Sajjadi,
Volume 12, Issue 1 (3-2015)
Abstract
High energetic aluminum nanoparticles are mainly used as additive in solid rocket propellants. However,
fabrication of these aluminized energetic materials is associated with decreasing the burning rate of propellants due
to problems such as oxidation and agglomeration of nanoparticles. In this study, to improve combustion performance
of aluminum nanoparticles, coating by metallic Ni shell was studied. Nickel coating of aluminum nanoparticles was
performed through electroless deposition (ED) subsequently, morphology and chemical composition of Ni-coated
nanoparticles were characterized by scanning electron microscopy (SEM), transmission electron microscopy (TEM),
energy dispersive spectroscopy (EDS) and X-ray diffraction (XRD). These studies show that a uniform Ni layer with a
thickness of 10nm is coated on the surface of Al nanoparticles. Thermal analysis of uncoated and Ni-coated aluminum
nanoparticles was done using differential thermal analysis (DTA) and thermo gravimetric analysis (TGA). The results
of thermal analysis indicate that, coating the aluminum particles by Ni, leads to improvement in combustion
performance of aluminum nanoparticles through decreasing critical ignition temperature, ignition delay time of the
nanoparticles and promoting the ignition by exothermic chemical reactions between Al and Ni
R. Khoshhal, M. Soltanieh, M. A. Boutorabi,
Volume 13, Issue 1 (3-2016)
Abstract
Al2O3/TiC composites are used as cutting tools for machining gray cast iron and steels. The addition of iron improves the toughness of Al2O3/TiC composites. Ilmenite, aluminum and graphite can be used to produce in-situ Al2O3/TiC–Fe composites. However, the formation mechanism and reaction sequences of this system are not clear enough. Therefore, the present research is designed to determine the reactions mechanism of the first step of reactions that may be occurred between raw materials. In this research, pure ilmenite was synthesized to eliminate the effects of impurities available in the natural ilmenite in the system. The milled and pressed samples, prepared from the synthesized ilmenite, aluminum and graphite mixture with a molar ratio of 1:2:1, were heat treated at 720°C for 48h. In addition, two samples one containing ilmenite and aluminum with a molar ratio of 1:2 and ilmenite and graphite with a molar ratio of 1:1 were heat treated at 720°C for 48h. The final products were analyzed with XRD. It was found that at 720°C, aluminum reacts with FeTiO3, forming Fe, TiO2 and Al2O3. Since the aluminum content used in the mixture was more than the stoichiometry for reaction of ilmenite and aluminum, some unreacted aluminum remains. Therefore, the residual aluminum reacts with the reduced Fe to form Fe2Al5.
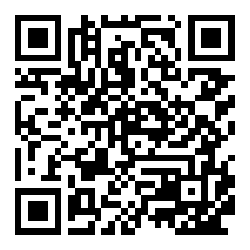
M. Soltanieh, M. Kiani, M. Hasheminiasari,
Volume 14, Issue 2 (6-2017)
Abstract
- The mechanism of diffusion layer growth in plasma nitrided coatings applied on a St52 steel using an active screen is investigated. The nitriding was performed at 450,500 and 550 ◦C temperature nitriding times of 5, 10 and 15 h, in a gas mixture containing 20 vol. % H2: 80 vol. % N2 and DC-pulsed plasma nitriding unit.
The surface, cross section and the thickness of diffusion of specimens was studied in terms of optical and scanning electron microscopy. According to the measurements of diffusion layer thickness, values of Q and D0 for nitrogen diffusion in substrate were calculated as 50585 (j/mol) and 4.11×10-10 (m2/s)respectively. The variations of depth of hardness during nitriding period was determined
Razieh Khoshhal, Seyed Vahid Alavi Nezhad Khalil Abad,
Volume 20, Issue 1 (3-2023)
Abstract
- In this article, the effect of graphite on iron-silicon interactions was investigated. It was found that, as graphite enters the iron structure, it permits further development of iron-silicon reactions. It was found that in the stoichiometric ratio of 1:0.5 of iron and silicon, when graphite is added to the system, simultaneously with the reaction of iron and silicon to form Fe3Si5, some amount of carbon can be dissolved in the iron and lead to more diffusion in iron and more iron silicide production. Silicon also reacts with carbon and produces SiC. The more amount of carbon entered into the system, the more growth of SiC occurs, while the production of other iron silicide phases, namely FeSi and Fe3Si preceded. Finally diffused carbon into the iron reaches a definite amount that can form Fe3C. In the stoichiometric ratio of 1:1 of iron and silicon, the formation of FeSi and SiC phases is observable. At the same time, the diffusion of carbon occurs in the same as the previous stoichiometric ratio. In the stoichiometric ratio of 1:2 of iron and silicon, compared with the stoichiometric ratio of 1:1, a larger amount of silicon is available and, the FeSi2 phase can form in addition to FeSi
Hamed Nadimi, Hossein Sarpoolaky, Mansour Soltanieh,
Volume 20, Issue 4 (12-2023)
Abstract
In the present investigation, an attempt was made to evaluate the dissolution behavior of Ti in molten KCl-LiCl. The X-ray diffraction (XRD) pattern of heated Ti plate at 800 oC for 4 h without carbon black in molten salt revealed that TiCl3 formation was feasible. For more assurance, Ti plate was heated at 950 oC for 4 h in the presence of carbon black to identify synthesized TiC. Transmission electron microscope (TEM) and scanning electron microscope (SEM) images from precursors and the final product showed that nano-crystalline TiC formation from coarse Ti particles was almost impossible without Ti dissolution. Thermodynamics calculations using Factsage software proved that it was possible to form various TiClx compounds. The TiC formation mechanism can be discussed in two possible ways: a reaction between Ti ion and carbon black for synthesizing TiC (direct) and a reaction between TiCl4 and carbon black led to indirect TiC synthesis. Elemental mapping using energy dispersive X-ray spectroscope (EDS) indicated that up to 815 oC, chlorine existed in the map.