H. R. Sobhani Kavkani, A. Mortezaei, R. Naghizadeh,
Volume 13, Issue 2 (6-2016)
Different mineral admixtures of Indian metakaolin, Iranian silica fume and nanosilica were used to produce high performance mortars. Two different sands types with grain size of 0.015-4mm were mixed with type II Portland cement, polycarboxylate superplasticizer,mineral admixture with 650kg/m3 cement content and water/cement ratio of 0.35. Different amount of cement was replaced by metakaolin or silica fume (5-15wt%) or nanosilica (0.8-5wt%). After mixing, moulding and curing, compressive strength, electrical resistivity and abrasion resistance were studied. The maximum compressive strength of 28 days samples were 76MPa, 79MPa and 75MPa for 15wt% substitution of cement with metakaolin, silica fume and 5wt% with nanosilica. The compressive strength of these samples showed 28%, 33% and 26% increment in comparison with reference sample, respectively. X-ray patterns showed that replacing silica fume leads to reduction of Portlandite (Ca(OH)2) phase. This can be attributed to the pozzolanic reaction and formation of new hydrated calcium silicate phase (CSH) that caused improvement of strength of admixtures containing samples. The microstructure of silica fume containing sample also showed better bond between sand and matrix. The electrical resistivity of samples with 15wt% metakaolin or silica fume and 5wt% nanosilica reach to 21kΩ.cm, 15 kΩ.cm and 10kΩ.cm, respectively. These samples showed high durability and corrosion resistance relative to reference samples (3.4 kΩ.cm). The abrasion resistance of different admixtures, specially silica fume containing samples were improved.
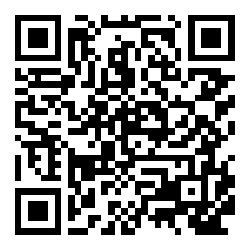