Showing 15 results for Coatings
M. Kazemi Pour, S. Sharafi,
Volume 5, Issue 1 (3-2008)
Abstract
Abstract: Hardfacing is one of the most useful and economical ways to increase the service life of
components subjected to abrasive wear. Iron based hardfacing alloys have long been considered
as candidate coatings for wear-resistant applications in industry. In the present work two layer of
Fe-34Cr-4.5C%wt hardfacing alloy was deposited on ASTM A36 carbon steel plates by SMAW
method. The microstructure consists of large primary and eutectic M7C3 carbides, metastable
austenite and small amount of secondary carbides. The microstructure was analyzed by optical
and scanning electron microscopes. In the same condition of size, shape, distribution and volume
fraction of carbides the as-welded matrix changed to martensite, tempered martensite and ferrite
by heat treatment processes. The wear resistance was measured by pin-on-disk method under loads
of 5, 10 and 20N and for sliding distance of 1500m. The results showed that the as-welded sample
with austenitic matrix has the most and the ferritic matrix specimen has the least wear resistance.
The predominate mechanisms for mass losses were determined to be micro-cutting, microploughing.
J. Saaedi, H. Arabi, Sh. Mirdamadi, Th. W. Coyle,
Volume 5, Issue 4 (12-2008)
Abstract
Abstract: Two different coating microstructures of Ni-50Cr alloy were obtained on a stainless steel substrate by
changing combustion characteristics of a high velocity oxy-fuel (HVOF) process and the size distribution of feed
powder during coating process. Use of the finer feed powder and leaner fuel in oxygen/fuel ratio (i.e. using a ratio
much less than stoichiometric ratio) led to formation of an extremely dense coating with high oxide content. Heat
treating of this coating at 650ºC for 4 hours caused the formation of an intermetallic sigma phase having Cr7Ni3
stoichiometry. Formation of this phase has been reported occasionally in thin films not in thermal spray coatings, as
reported for the first time in this research. In addition no sigma phase was detected in the HVOF as-deposited coating
with low oxide content after heat treatment of the samples. Therefore, due to the limited number of papers available in
the subject of formation of phase in either Ni-Cr bulk alloys or coatings, it is considered appropriate to show up a
case in this field. In this work, the formation of sigma phase in Ni-50Cr coating deposited by HVOF technique and
heat treated at 650ºC was discussed and then the coating was characterized.
A.m. Rashidi, A. Amadeh,
Volume 7, Issue 2 (6-2010)
Abstract
Abstract:
nanocrystalline nickel samples with the grain size of ~25 nm were prepared via direct current electrodeposition and
aluminized for different durations by pack cementation method at 500
means of SEM, EDS and XRD techniques. According to results, short time aluminizing resulted in the formation of a
single aluminide layer whereas at long duration two distinct aluminide layers were formed. The growth kinetics of the
coating was non-parabolic at short times while it obeyed the parabolic law at long duration. The parabolic growth
rate constant of single phase coating formed on electrodeposited samples was about 30 ìm / h1/2 approximately 3 times
greater than the data reported for coarse grained nickel (8.4 ìm / h1/2). Meanwhile, the overall growth rate constant
was decreased to 11.7 ìm / h1/2, when double aluminide layers formed on nanocrystalline nickel.
In this research, aluminizing behavior of ultra fine-grained nickel was investigated. For this purpose,oC. The aluminide layers were examined by
H. Arabi, S. Rastegari, V. Ramezani, Z. Valefi,
Volume 10, Issue 2 (6-2013)
Abstract
The objectives of this research were to find an economical way of reducing porosities in the microstructure of coatings deposited by flame spraying technique on CK45 steel and also trying to increase their cohesive strength to the substrate, so that the overall wear properties of this type of coating can be improved. So several specimens from this steel coated with NiCrBSi powder under specific conditions were subjected to various furnace heat treatment at 1000, 1025, 1050, 1075 and 1100 °C, each for periods of 5, 10 and 15 minute before cooling them in air. Tribological properties of treated coatings were evaluated by pin on disc method. The results show the highest wear resistance and microhardness values observed in one of the sample was due to lower amount of porosity and higher amount of very fine Cr2Ni3B6 particles precipitated homogeneously throughout its microstructure during specific heat treatment.
M. Bahamirian, Sh. Khameneh Asl,
Volume 10, Issue 3 (9-2013)
Abstract
In the present study NiCrAlY bond coating layer was produced by electroplating against common atmospheric plasma spraying (APS). Both types of the bond coats were applied on IN738LC base metal then, the YSZ (ZrO2-8% Y2O3) thermal barrier top layer was coated by atmospheric plasma spray technique. Hot corrosion is one of the main destructive factors in thermal barrier coatings (TBCs) which come as a result of molten salt effect on the coating–gas interface. In this investigation the hot corrosion behavior of coatings was tested in the furnace which was contain Na2SO4-55% V2O5 and mixed salts environment at 900°C up to 15 hr. dwell time. Optical microscopy, scanning electron microscopy (SEM / EDS) and X-ray diffraction analysis (XRD) was used to determine the crystallographic structure and phase transformation of the coatings before and after the hot corrosion tests. The transformation of tetragonal Zirconia to monoclinic ZrO2 and formation of YVO4 crystals as hot corrosion products caused the degradation of mentioned TBCs. The results showed NiCrAlY coated by economical electroplating method a viable alternative for common thermals sprayed bond coats in hot corrosive environments with same corrosion behavior
A. Yazdani, R. Zakeri,
Volume 12, Issue 2 (6-2015)
Abstract
In this paper, the possibility of mechanical coating of aluminum with either Ni or SiC using planetary ball
mill was studied. The Al substrate was fixed inside of the vial lid of a planetary ball mill filled with milling balls and
starting powder. The phase analysis and crystallite size measurement of the coatings were carried out using X-ray
diffraction (XRD) method. Scanning electron microscope (SEM) was employed to study the coating/substrate interface
and coating thickness. Hardness and wear resistance of coatings were also measured. The results indicated that all
coatings have relatively uniform thickness. SiC coating shows poor compaction and adhesion to the Al, while nanostructured Ni coating is well-bonded to the substrate. Moreover, Ni coating showed higher hardness and wear
resistance compared to SiC coating. It was found that the balls collision will result in the grain refinement of the
coating as well as Al substrate. Mechanically deposited Ni coating shows higher hardness value compared to those
obtained by conventional methods. This has been related to the induced grain refinement phenomenon.
M. R. Khorram, M. R. Shishesaz, Iman Danaee, D. Zaarei,
Volume 13, Issue 1 (3-2016)
Abstract
The micro layers micaceous iron oxide and nano-TiO 2 were incorporated into the epoxy resin by mechanical mixing and sonication process. Optical micrographs showed that the number and diameter size of nanoparticle agglomerates were decreased by sonication. The structure and composition of the nanocomposite was determined using transmission electron microscopy which showed the presence of dispersed nano-TiO 2 in the polymer matrix. The anticorrosive properties of the synthesized nano-composites coating were investigated using salt spray, electrochemical impedance spectroscopy and polarization measurement. The EIS results showed that coating resistance increased by addition of micaceous iron oxide micro layers and nano-TiO 2 particles to the epoxy coatings. It was observed that higher corrosion protection of nanocomposite coatings obtained by the addition of 3 %wt micaceous iron oxide and 4%wt nano-TiO 2 into epoxy resin.
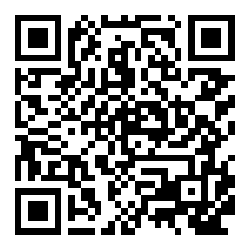
M. S. Mahmoudi Jozee, S. Sanjabi, O. Mirzaee,
Volume 13, Issue 3 (9-2016)
Abstract
A homogenous TiO2 / multi-walled carbon nanotubes(MWCNTs) composite film were prepared by electrophoretic co-deposition from organic suspension on a stainless steel substrate. In this study, MWCNTs was incorporated to the coating because of their long structure and their capability to be functionalized by different inorganic groups on the surface. FTIR spectroscopy showed the existence of carboxylic groups on the modified carbon nanotubes surface. The effect of applied electrical fields, deposition time and concentration of nanoparticulates on coatings morphology were investigated by scanning electron microscopy. It was found that combination of MWCNTs within TiO2 matrix eliminating micro cracks presented on TiO2 coating. Also, by increasing the deposition voltages, micro cracks were increased. SEM observation of the coatings revealed that TiO2/multi-walled carbon nanotubes coatings produced from optimized electric field was uniform and had good adhesive to the substrate.
T. Ebrahimi Sadrabadi, S.r. Allahkaram, N. Towhidi,
Volume 13, Issue 4 (12-2016)
Abstract
Porous hollow glass microspheres have many uses, including encapsulation of active materials. In this paper a fast and facile method for fabricating porous hollow glass-microspheres was demonstrated by etching them using dilute hydrofluoric acid. Then, a highly reactive amine was infiltrated into the etched glass microspheres. Scanning electron microscopy was conducted for the hollow glass microspheres prior and post etching process. With regards to the porous hollow glass spherical sample, the spherical nature, morphology, pore diameter and the porosity were studied using scanning electron microscopy. Formation of the intact hollow glass microspheres with an open through wall porosities following phase separation and etching of the boron oxide rich phase was demonstrated using reciprocating shaker as the most suitable agitation method. The BET results indicated that the surface of the porous microspheres contained nano-pores. It is believed that the simplicity of the reported fabrication technique of micro/nano porous structure has the potential to scaling up for large scale production
Z. Valefi, M. Saremi,
Volume 14, Issue 2 (6-2017)
Abstract
In this paper the effect of plasma spray parameters, atomizing gas and substrate preheat temperature on microstructure and phase composition of YSZ coatings produced by SPPS process have been investigated. The experimental results showed that increasing the power of plasma, using hydrogen as the precursor atomizing gas and increasing substrate preheat temperature decrease the amount of non-pyrolyzed precursor in the coatings. At low plasma power most of the deposited precursor is in non-pyrolyzed state, and consequently the applied coatings are defective. The increase in substrate temperature beyond 800oC either by preheating or heat transfer from plasma torch to the substrate, prevent the coating formation. In SPPS coating formation, up to a special spray distance the optical microscopy image of the coatings showed a snowy like appearance. XRD analysis showed that in this situation the amount of un-pyrolyzed precursor is low. Beyond this spray distance, spherical particles, are obtained and XRD analysis showed that most of the precursor is in un-pyrolyzed state.
F. Sousani, R. Mozafarinia, A. Eshaghi, H. Jamali,
Volume 15, Issue 1 (3-2018)
Abstract
In this research, Germanium-carbon coatings were deposited on ZnS substrates by plasma enhanced chemical vapor deposition (PECVD) using GeH4 and CH4 precursors. Optical parameters of the Ge1-xCx coating such as refractive index, Absorption coefficient, extinction coefficient and band gap were measured by the Swanepoel method based on the transmittance spectrum. The results showed that the refractive index of the Ge1−xCx coatings at the band of 2 to 2.2 µm decreased from 3.767 to 3.715 and the optical gap increased from 0.66 to 0.72 eV as CH4:GeH4 increases from 10:1 to 20:1.
S. Akbarzadeh, S.r. Allahkaram, S. Mahdavi,
Volume 15, Issue 2 (6-2018)
Abstract
Tin-Zinc alloy coatings have many applications because of their unique properties such as corrosion resistance, solderability and flexibility. In this study, the effect of current density, temperature and pH on chemical composition, cathodic current efficiency, morphology and structures of the coatings was investigated. The results illustrated that, at low current densities (<0.5 mA/cm2), the coatings were relatively pure tin, but Zn content increased with enhancing the current density. At higher currents a relatively pure Zn film was obtained. Temperature and pH also affected chemical composition of the alloy films. Zn content of the coatings was decreased by increasing the temperature, while its variation with pH had ascending-descending trend. Morphological investigation of the coatings revealed that increasing Zn content of deposits led to porous, rough and fine grained films.
Farid Lekmine, Hachemi Ben Temam, Elhachmi Temam,
Volume 18, Issue 3 (9-2021)
Abstract
Nickel phosphorus alloy coatings were prepared by electrodeposition route from sulfate electrolyte bath at various current densities. SEM studies reveal spherical grains covered the entire surface with uniform distribution. EDX results showed a linear increase of P content in the developed deposits with current density and therefore, enhancing the grains size and drop of the hardness values. XRD studies reveal monocrystalline orthorhombic alloys at a low amount of phosphorus (10.88 wt. %). Corrosion tests show that 1 A.dm-2 is the best applied current density giving the nobler Ecorr (-171.4 mV) and the lower icorr (4.64 µA/cm2).
Pooyan Soroori, Saeid Baghshahi, Arghavan Kazemi, Nastaran Riahi Noori, Saba Payrazm, Amirtaymour Aliabadizadeh,
Volume 19, Issue 3 (9-2022)
Abstract
The goal of the present study is to prepare a room temperature cured hydrophobic and self-cleaning nano-coating for power line insulators. As a result, the installed insulators operating in power lines can be coated without being removed from the circuit and without the need to cut off power. For this purpose, hydrophobic silica nanoparticles were synthesized by sol-gel method using TEOS and HMDS. The synthesized hydrophobic silica nanoparticles were characterized by XRD, FTIR, SEM, and TEM analyses to investigate phase formation, particle size, and morphology. Then the surface of the insulator was cleaned and sprayed by Ultimeg binder solution, an air-dried insulating coating, as the base coating. Then the hydrophobic nano-silica powder was sprayed on the binder coated surface and left to be air-cured at room temperature. After drying the coating, the contact angle was measured to be 149o. Pull-off test was used to check the adhesion strength of the hydrophobic coating to the base insulator. To evaluate the effect of environmental factors, UV resistance and fog-salt corrosion tests were conducted. The results showed that 150 hours of UV radiation, equivalent to 9 months of placing the samples in normal conditions, did not have any significant effect on reducing the hydrophobicity of the applied coatings.
Fabio Edson Mariani, Gabriel Viana Figueiredo, German Barragan, Luiz Carlos Castelleti, Reginaldo Teixeira Coelho,
Volume 20, Issue 3 (9-2023)
Abstract
Elevating component performance through advanced surface coatings finds its epitome in the domain of laser cladding technology. This technique facilitates the precision deposition of metallic, ceramic, or cermet coatings, accentuating their superiority over conventional methods. The application spectrum for laser-clad metallic coatings is extensive, encompassing critical components. Central to the efficacy of laser cladding is the modulation of laser parameters—encompassing power, speed, and gas flow—which decisively influence both process efficiency and coating properties. The meticulous calibration of these parameters holds the key to producing components endowed with refined attributes while ensuring the sustainable continuation of the process. As such, this study embarks on an empirical investigation aimed at transcending existing process limitations. It delves into the characterization of laser-clad WC-17Co coatings on AISI H13 and AISI 4140 steels. The importance of WC-17Co coatings lies in their capacity to enhance wear resistance, extend component life, reduce maintenance costs, and improve the performance of various industrial components across diverse sectors. On the other hand, the substrates have pivotal roles. AISI H13 is lauded for its exceptional hot work capabilities, while AISI 4140 steel is renowned for its robust strength and endurance. Through rigorous evaluation, the resultant deposited coatings offer crucial insights into the efficacy of manufacturing parameters. Employing a comprehensive suite of analytical techniques including laser confocal microscopy, Vickers microhardness assessment, and micro-adhesive wear testing, the study thoroughly characterizes the samples. The outcomes underscore the achievement of homogenous coatings marked by elevated hardness and exceptional wear resistance, thereby signifying a substantial enhancement over the substrate materials.